Industrial inspection robots are mobile data-gathering systems: they carry measurement sensors and are designed to navigate facilities built for humans. The usage of this technology is rapidly growing, yet comparing different robotic inspection offerings can be overwhelming. It involves knowing why you require the technology, considering the suitability of an entire solution, i.e., looking beyond the physical robotic carrier platform, evaluating the solution from an end-to-end perspective, and ultimately partnering with an enterprise-level vendor.
If you are interested in using ground robots to automate industrial inspection jobs in your plant operations, this three-part article series is for you:
- Identify the task you want to automate
-
Find the right inspection robots for your facilities
- Ensure data integration and safety features
They will equip you to evaluate different platforms, understand the industrial inspection ecosystem, and make informed decisions around requirements, applications, and suitability.
This article focuses on the second step in this selection process: finding suitable robots for your facilities’ environments.
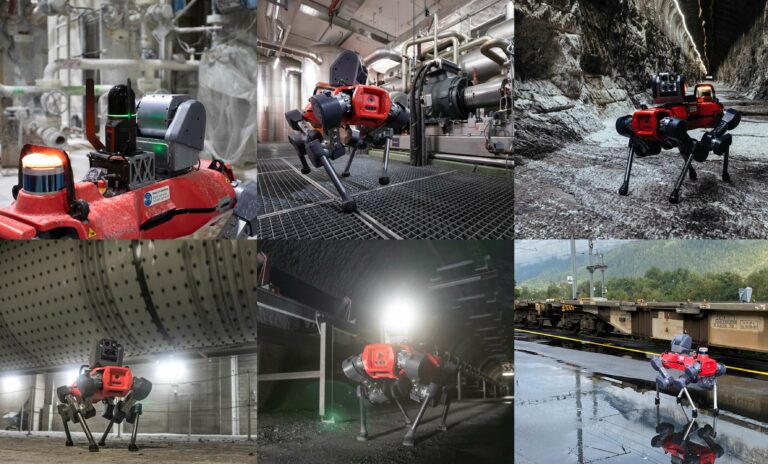
Different Inspection Robots Suit Different Environments
After defining which type of task we want to automate, it is essential to think about “where” the robot will perform automated inspections.
Industrial sites vary in complexity, including stairs, multiple levels, Ex-rated zones, dark areas, outdoor facilities, and adverse weather conditions: the effectiveness of these inspection robots hinges significantly on their suitability for the diverse environments they encounter.
Understanding the specific navigation challenges inherent in industrial settings is essential for selecting the most suitable inspection robot. Below are some of the key navigation challenges faced by inspection robots in industrial environments:
Presence of Stairs
People design industrial plants for people, and they invariably have stairs, steps, and other obstacles, such as piping.
For large-scale automation of inspection tasks, robots must climb stairs and be able to overcome various obstacles on the ground. Ideally, robots have a small footprint and can move in all directions (omnidirectional) to get close to the machinery. Because passages are often very narrow, robots usually provide a symmetric design to move bidirectionally, i.e., forward or backward, without turning around.
Different robotic inspection platforms are better suited to distinct types of terrains.
Robots with wheels or tracks are physically limited to flat surfaces, while some systems provide so-called “flippers” that enable them to overcome moderate terrain with small steps. Robots that move on legs offer maximum flexibility: robots like ANYmal, for example, can climb stairs, easily overcome steps, piping, and other obstacles, and reliably move in gravel, sand, grass, and snow.

Complex Environment
Industrial environments often contain complex machinery, piping systems, and other obstacles that can obstruct the path of inspection robots.
The robot’s ability to locate itself – using Lidar, depth cameras, and sensors – and plan a new route when encountering unforeseen obstacles is critical.
Some systems can get ‘lost’ or confused more easily than others and require additional artificial markers (AR tags) to be set up in the environment. Other systems provide advanced autonomy that robustly localizes the robot, providing reliable path optimization and navigation, even in adverse weather conditions and harsh environments such as the open sea.
Leading solutions are designed to navigate existing facilities and require no additional structural changes.
ANYbotics – Unparalleled autonomy and global path optimization
The ANYbotics autonomy stack Pharos is optimized to provide ANYmal with unparalleled autonomy in even the toughest environments.
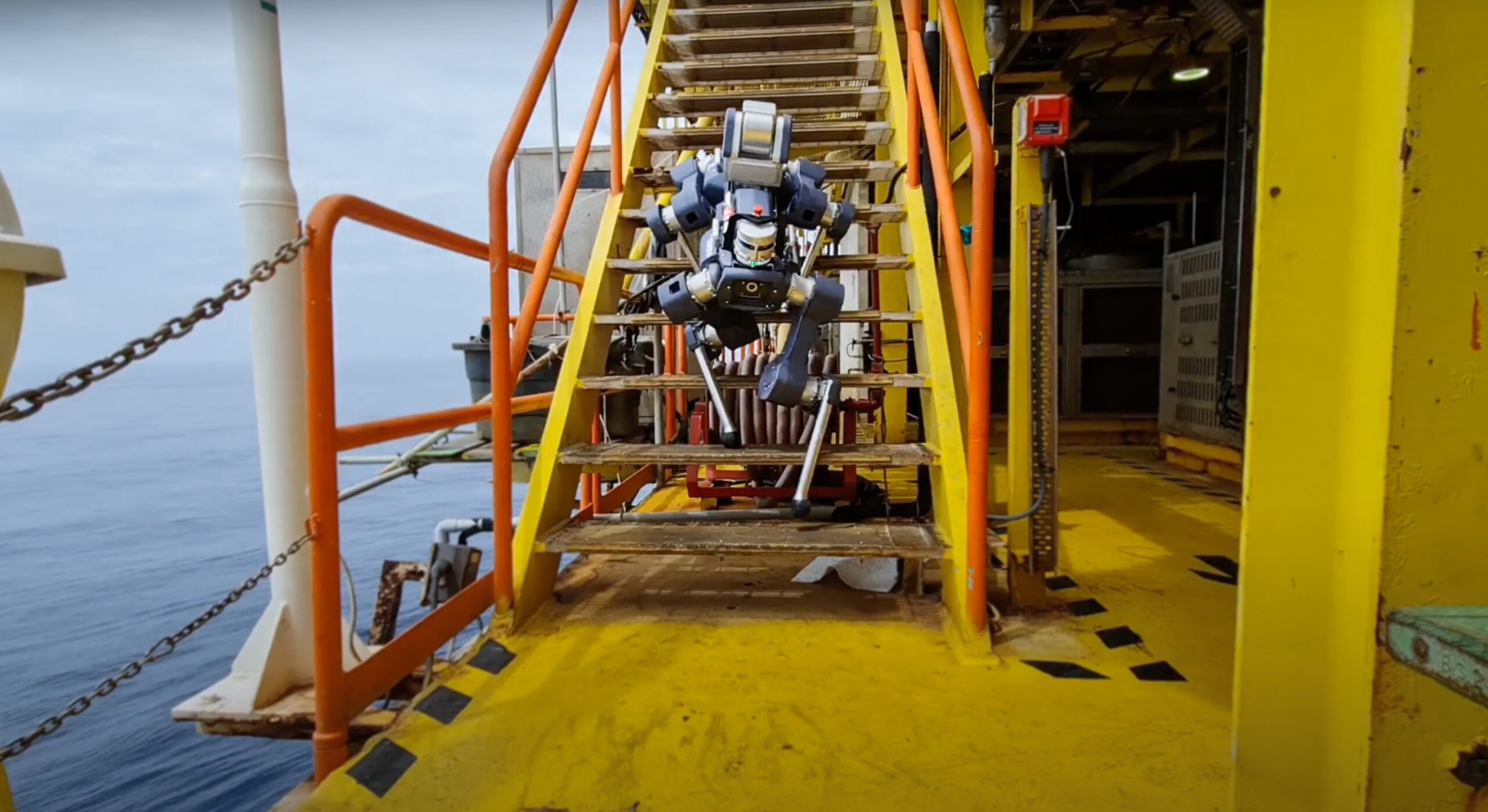
ANYmal X performing an automated inspection mission at an offshore oil & gas facility. (Courtesy: PETRONAS)
Data Connection Missing
Most industrial plants can only provide partial wireless data connectivity throughout the facility. This means that the robotic solution needs to operate without a permanent data connection.
Leading inspection robots carry built-in computing capabilities, have onboard data storage, and upload the data once they connect to an available network. This functionality eliminates the need for continuous network communication and allows the robot to operate effectively without WiFi or cellular connection.
For example, ANYmal provides full autonomy and continuous data collection independently of a stable network connection but can leverage a WiFi and 4G/LTE interface for real-time reporting and teleoperation.
Harsh Conditions
Outdoor inspections present several challenges, including rain, humidity, dust, and salt water. Robotic solution providers rate their inspection robots according to the ISO Standard for Ingress Protection (IP Code), which indicates how well a device is protected against liquids and dust. An IP67 rating is the standard for outdoor inspection robots because it allows for continuous long-term use in outdoor environments without the risk of damaging the system.
Due to the nature of industrial sites, inspection robots can accumulate a variety of undesirable substances, including hydrocarbons, chemical residues, and radioactive dust. It is important that robots can be easily cleaned and decontaminated of toxic or active substances without compromising functionality. For example, robots with an IP67 ingress protection rating can be cleaned quickly and easily with high-pressure water.
ANYmal – Ruggedized design
Robust design is a prerequisite for full functionality in harsh, wet and dirty conditions. ANYmal is 100% protected against dust and water and can be easily cleaned with water after inspection missions.
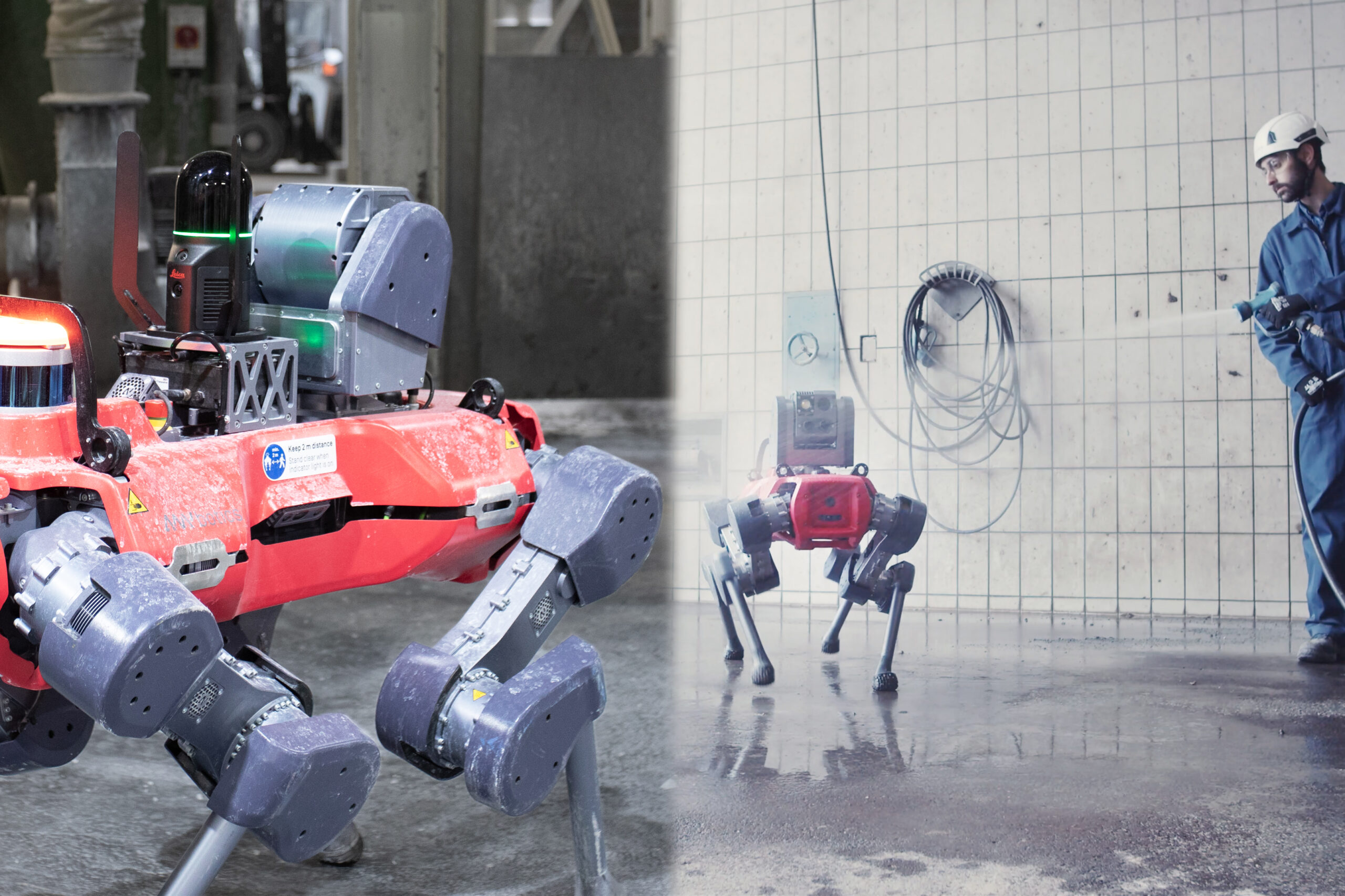
ANYmal’s robust design and IP67 rating are essential for full functionality in harsh, wet, and dirty conditions.
Size of Coverage Area
The size of the coverage area poses a significant navigation challenge for inspection robots, particularly in extensive industrial facilities spanning expansive areas. The effectiveness of an inspection robot is closely tied to its ability to monitor a wide range of inspection points within the facility. However, the robot’s operational range, determined by factors such as battery life and recharge time, can limit its ability to cover large distances without interruption.
For instance, legged and tracked robots can cover different areas and are more suitable for various environments.
Tracked robots are relatively heavy, some weighing more than 100 kg. They can have a battery life of up to 4 hours and a 2-3 km range. Because of their relatively slow speed, short range, and inability to climb industrial stairs, tracked robots are primarily suited for relatively flat environments.
Conversely, legged robots are comparatively light at around 55 kg or less. They typically have a battery life of 2 hours and a range of up to 4 km. Because of their comparatively higher speed, longer range, and ability to climb industrial stairs, legged robots provide complete coverage and are well-suited for flat and complex environments.
Ex-rated Zone Presence
Environments where flammable or explosive gasses or liquids are handled are defined as Ex-rated.
Most areas in Oil & Gas and Chemical facilities are Ex-rated, and operators require Ex-certified, intrinsically safe equipment in these zones (ATEX or IECEx certification, for example). Ex-rated areas are classified into zones (Zone 0, Zone 1, or Zone 2) based on the occurrence and duration of explosive atmospheres. Zone 1 certification is typically required to get inspection robots near the equipment.
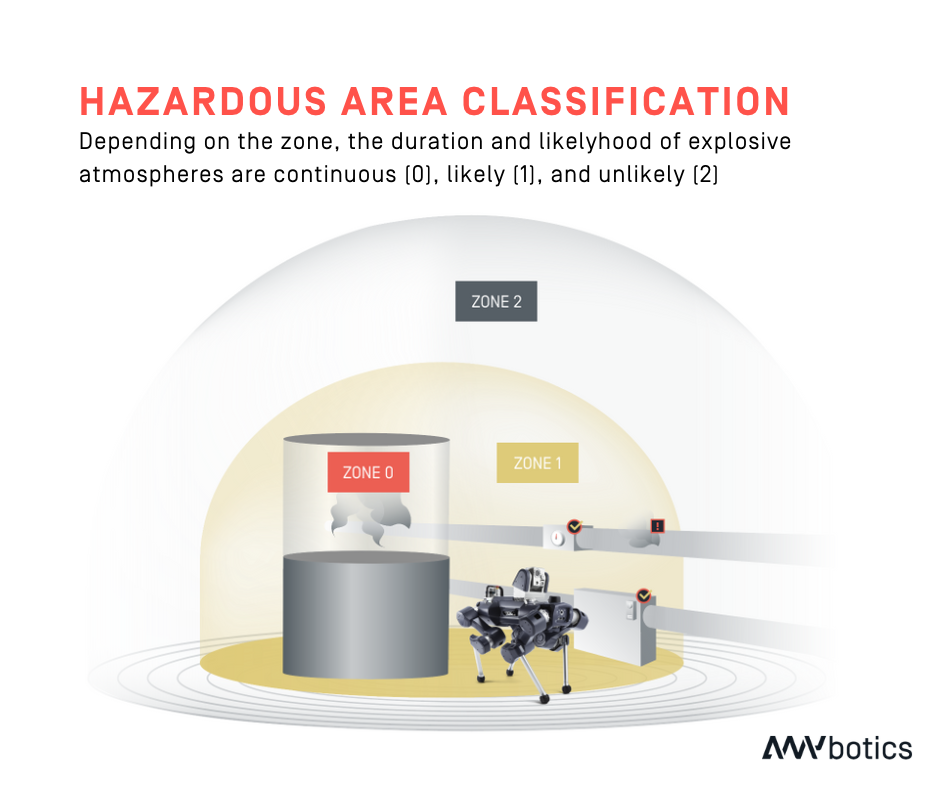
Several inspection robots are Ex-certified, such as ExRobotics’ ExR-2, Taurob’s Inspector, and ANYbotics’ ANYmal X. Certification classes differ, so it is essential to check that the robot’s certification is compatible with your facility. Both the ATEX and IECEx certifications align with the IEC 60079 standards, and as the marking systems are very similar, they are often combined. See the Hazardous Area Guide for a breakdown of ATEX and IECEx marking characters.
ANYmal X – Game changer for the Oil & Gas and Chemical industries
As the world’s only Ex-certified, legged robotic solution, ANYmal X is Ex-certified for Zone 1 usage according to the IECEx and ATEX standards.
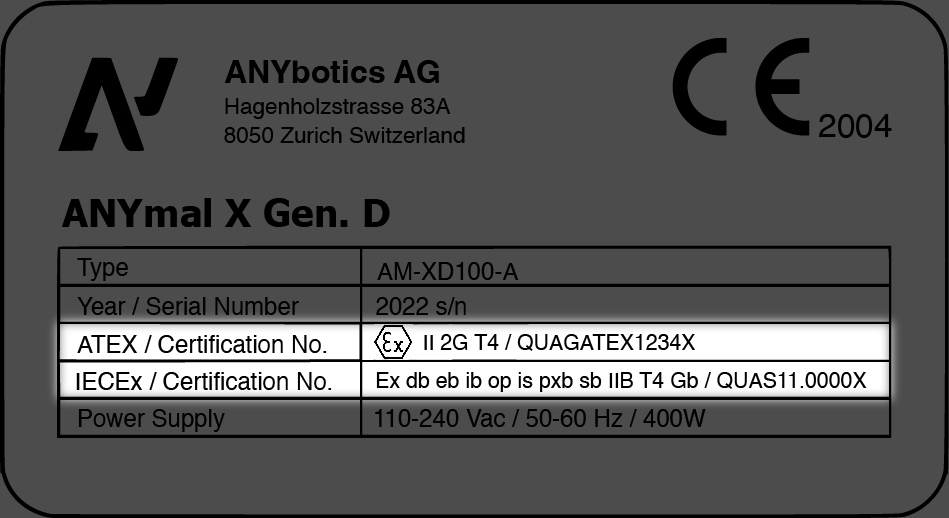
Night Shift
Some robots can effectively perform inspection tasks in dimly lit or dark environments, enabling 24/7 usage. Typical Lidar and active stereo cameras use active infrared (IR) lighting that is not visible to the human eye but enables the robot to see without external lighting. Top inspection robots use powerful LED spotlights to capture high-quality visual information for visual inspection in difficult lighting conditions.
ANYmal – Effective in complete darkness
Digital Realty, one of the leading carrier-neutral colocation providers, integrates ANYmal to monitor their HVAC systems continuously. ANYmal performs hundreds of inspections in hourly autonomous missions every day. Even in complete darkness, ANYmal performs effectively. No additional lighting is required for ANYmal to deliver frequent and reliable inspection results.
Examples of Inspection Robots Tailored to Different Environments
Based on environmental requirements, we can group the most renowned autonomous robots in industrial inspections.
Boston Dynamics’ highly mobile Spot (IP54 rating) is suitable for indoor and outdoor areas with temperate weather conditions. Unitree’s B1 (IP68 rating) and ANYbotics’ ANYmal (IP67 rating) can operate outdoors in adverse weather conditions, but only ANYmal can negotiate stairs autonomously.
When it comes to hazardous and potentially explosive areas, which are ubiquitous in the Oil & Gas and Chemical industries and require intrinsically safe equipment with ATEX/IECEx certification, only three currently available robots meet the certification requirements:
-
- ExRobotics’ tracked ExR-2 (IP67 rating), which navigates on flat surfaces;
- Taurob’s Inspector (IP67 rating) with flexible tracks that can negotiate stairs;
- ANYbotics’ ANYmal X (IP67 rating) is the only legged robot that can navigate complex multi-story facilities.
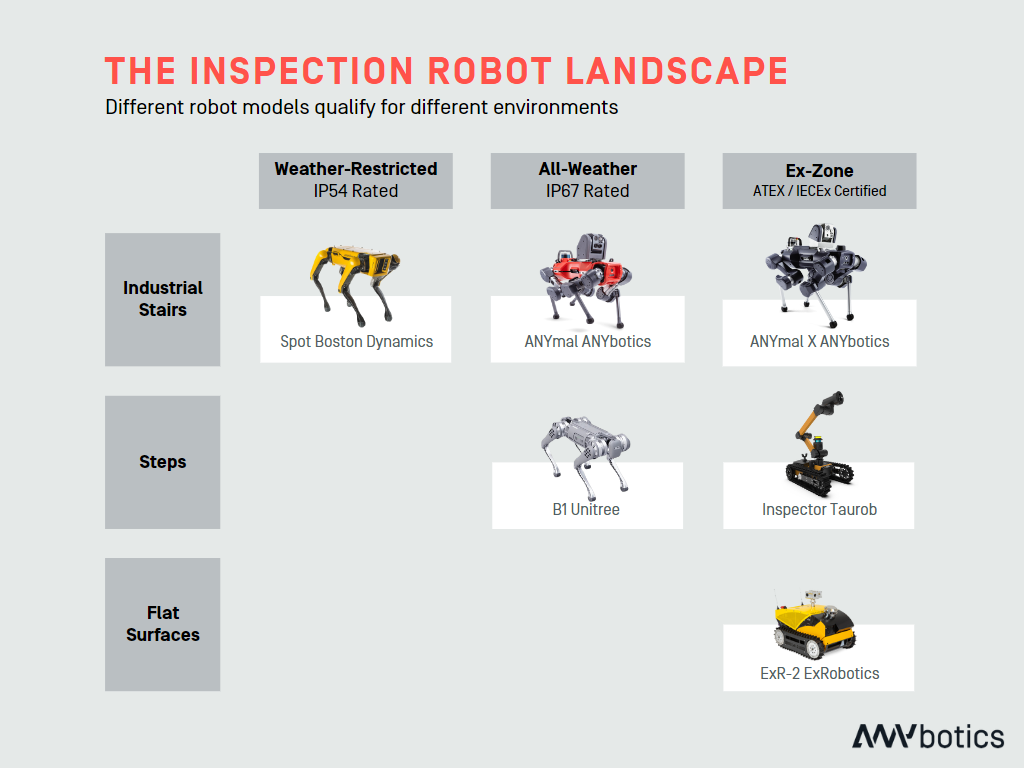
Looking Ahead
By understanding the unique capabilities and limitations of each type of inspection robot, businesses can make informed decisions when selecting the most suitable solution for their specific industrial environment.
Whether navigating through confined spaces, accessing elevated areas, or in hazardous situations, choosing the right type of robot ensures efficient and effective inspections tailored to the application’s demands.
Start your robotic journey with ANYbotics
Get a glimpse of the value ANYmal can unlock
for your business with this 30-minute demo: