In today’s rapidly evolving industrial landscape, a complete solution to the challenges of inspection and maintenance is emerging: inspection robots.
These mobile machines, equipped with advanced sensors, autonomous navigation systems, and cutting-edge technologies, are transforming how industries conduct inspections as they increasingly seek safer, more cost-effective, and more efficient ways of completing these routine tasks.
In this article, we delve into the world of industrial inspection robots, exploring their nature, key features, and applications.
Whether you’re a beginner seeking to understand the fundamentals of inspection robotics or a seasoned professional looking to stay ahead of the curve, this article provides a comprehensive guide to unlocking the potential of these transformative technologies.
Table of contents:
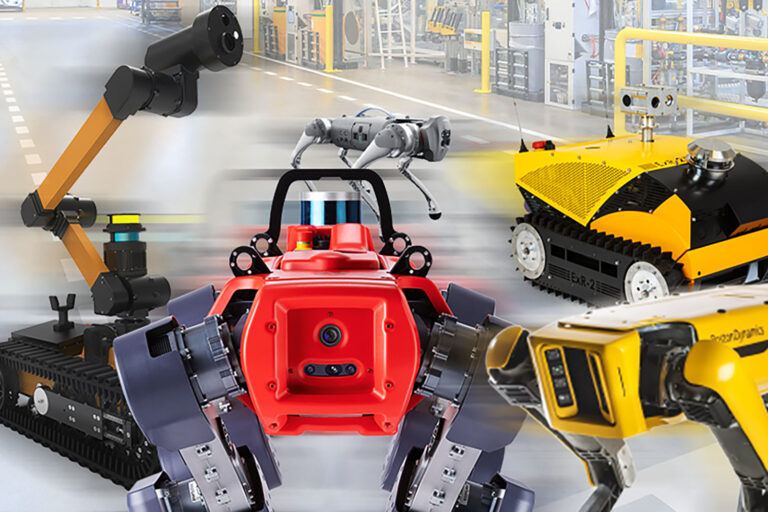
What is an Inspection Robot?
An inspection robot is a versatile machine equipped with software, sensors, vision systems, and other advanced technologies to interact with the surrounding environments, gather data, and perform routine or critical inspection tasks.
Inspection tasks are frequent in many industrial environments (refineries, power plants, offshore platforms, minings, or power stations), and their main purpose, besides checking and monitoring, is to detect malfunctions and errors.
Many of these environments present danger for humans. The robots’ abilities to access hazardous or hard-to-reach areas and their capacity for data collection and analysis have positioned them as indispensable assets across various sectors.
Types of inspection robots
The global market for inspection robots is growing every day, we listed the main types of inspection robots on the market:
-
-
- Aerial Drones: Aerial drones, also known as unmanned aerial vehicles (UAVs) or quadcopters, are probably the ones everyone thinks of when talking about robotic inspections. These lightweight, maneuverable devices are equipped with high-resolution cameras, thermal imaging sensors, and sometimes LiDAR technology. Aerial drones excel in inspecting large structures such as bridges, power lines, and rooftops, offering a bird’s-eye view of the area without the need for human intervention.
- Ground-based Robots: Ground-based inspection robots are designed to navigate various terrains, from smooth warehouse floors to rugged outdoor environments. These robots can be equipped with wheels, tracks, or even legs, allowing them to traverse obstacles and access confined spaces. Ground-based robots are commonly used for inspecting pipelines, storage tanks, industrial machinery, and infrastructure such as tunnels and sewers.
- Underwater Robots (ROVs): Underwater robots are specifically designed to inspect submerged structures and environments. These highly maneuverable robots are equipped with cameras, sonar systems, and sometimes manipulator arms to perform complex tasks and navigate challenging environments precisely.
- Crawler Robots: Crawler robots are specialized inspection devices designed to move along surfaces such as walls, ceilings, and vertical structures. Equipped with grippers or suction cups, crawler robots can adhere to various surfaces while carrying out inspections.
-
In turn, these types of robots can be divided based on the need for control by an operator. In fact, robot control can be of three types:
-
-
- Full autonomy: The robot doesn’t require human intervention to conduct everyday inspections.
- Supervised autonomy: The robot accomplishes short-term tasks under supervision or under the request of human supervision.
- Teleoperation: The robot is fully controlled by a human operator who guides the robot in unknown environments.
-
Moreover, different environments – the size of the space to be inspected, the presence of stairs and obstacles, indoor or outdoor, hazardous and potentially explosive areas – also might require different inspection robot solutions.
Comparing different inspection robotics can be overwhelming since the technology is rapidly and constantly changing.
The type of inspection tasks and the output data and insights you need can vary greatly, not only from industry to industry but from facility to facility. To understand which robots might be the best for your business, you should first determine which robotic inspection solutions meet your organization’s specific needs and ensure which type of inspection robot can bring you real value.
What are the advantages of robotic inspection
When it comes to industrial inspection, embracing robotic solutions offer distinct advantages over traditional methods:
-
-
- Improved safety for human workers: Due to the nature of industrial environments, inspection tasks are usually dangerous or difficult to access for humans. In addition, they usually require working outside operating hours and in extreme conditions. In these contexts, inspection robots quickly become invaluable allies in increasing worker safety with their ability to operate for extended durations and under challenging environmental conditions. In addition to keeping humans safe, robots can take care of mechanical and repetitive activities, allowing operators to focus on tasks that are of higher value and more stimulating.
- Increase productivity and cost-effectiveness: Automation technology also brings economic benefits. Firstly, they provide a substantial cost-saving opportunity, reducing the need for extensive human resources and associated expenses. Additionally, by regularly conducting inspections, these robots can identify signs of wear, corrosion, or other defects before they escalate into more significant problems. This early detection allows for timely intervention and preventive maintenance actions, minimizing the risk of costly downtime associated with unexpected equipment failures.
- Improved data accuracy and consistency for better data-driven decisions: Inspection robots generate vast amounts of data during the inspection process, including images, sensor readings, and other diagnostic information. By leveraging this data, organizations can gain valuable insights into the condition and performance of their assets. Furthermore, inspection robots ensure unparalleled data accuracy and consistency, eliminating human errors and providing reliable insights for informed decision-making.
- Resolve the workforce shortage problem: By 2030, more than 85 million jobs will likely be unfilled due to skills shortage. As Korny Ferry stated in his study, “The biggest issue isn’t that robots are taking all the jobs—it’s that there aren’t enough humans to take them.” Inspection robots hold a tremendous potential to alleviate labor shortages and increase productivity in the middle and long term.
-
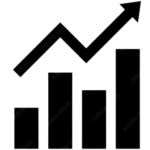
Increase productivity
Higher equipment uptime
Longer asset lifetime
Reduce production losses
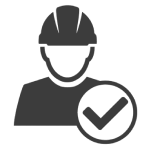
Improve safety & sustainability
Reduce hazardous exposure
Mitigate workforce shortages
Attract, retain & upskill workforce
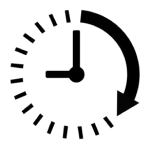
Optimize maintenance
Increase inspection cadence & accuracy
Conduct inspections during operation
Decrease inspection costs
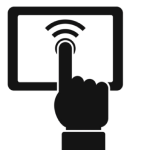
Accelerate digitalization
Create & maintain digital facility records
Digitalize manual processes
Enable predictive monitoring & maintenance
Technology and key features enabling robot inspection
Understanding the key features and technologies that empower inspection robots is essential for leveraging their effectiveness in various industrial settings. Most of the common technologies that enable inspections are:
- Advanced sensors include cameras, LiDAR (Light Detection and Ranging), and thermal imaging systems: these sensors enable them to capture detailed imagery, detect anomalies, and assess the condition of equipment and infrastructure with precision and accuracy.
- Autonomous navigation systems are another critical component of inspection robots, allowing them to navigate complex environments and perform inspections without human intervention. These systems utilize advanced algorithms and sensor data to navigate obstacles, follow predefined routes, and adapt to changing conditions, ensuring efficient and thorough inspections.
- Remote control and monitoring capabilities enable operators to oversee and control inspection robots from a safe distance. This feature is particularly beneficial in hazardous environments such as oil and gas, nuclear facilities, and chemical plants, where human access may be limited or dangerous.
- Furthermore, inspection robots are equipped with sophisticated data analytics and reporting tools, enabling them to analyze sensor data in real-time, identify trends, and generate comprehensive reports.
What are the applications of robotics inspection?
Inspection robots’ main application is automating routine inspections, making these operations significantly safer for human operators and more efficient than manual methods. Based on the technologies available – visual, thermal, and acoustic sensors, for example – robots can detect equipment failure early and take preventive maintenance action to avert costly defects and downtime.
Inspection robots are particularly marketed for:
- Monitor assets and equipment meanwhile in operations;
- Identify and report anomalies;
- Detect gas presence or gas leak;
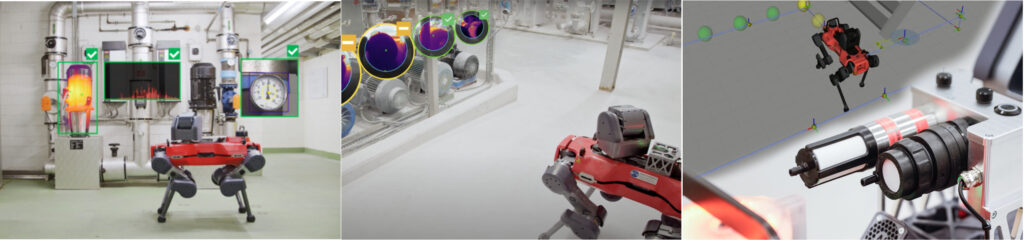
In addition, each industry has its own needs, and inspection tasks may vary according to these needs and focus on different tasks.
Within the oil and gas sector, for example, automated inspection equipment plays a vital role across various stages, given the intricate chemical processes involved and the complex machinery in use that makes manual inspections significantly risky. Operators might utilize robotic tools to detect gas leaks, crawl along pipelines to perform visual inspections, or monitor various instrumentation assets through thermal measurements.
Another example is power and utilities facilities, such high voltage power substations, where automated inspection tools play a crucial role in inspecting power lines and distribution infrastructure, ensuring the integrity and reliability of electricity transmission to consumers.
Obviously, the different applications are also linked to the type of robot and its intrinsic capabilities.
For example, some robots, like those with wheels or tracks, work best on flat surfaces but struggle with obstacles like stairs.
Legged robots, such as ANYmal, offer the most versatility: they can climb stairs, navigate obstacles like steps and pipes, which are usually common in chemical plants or move smoothly on wet and bumpy terrains like underground minings.
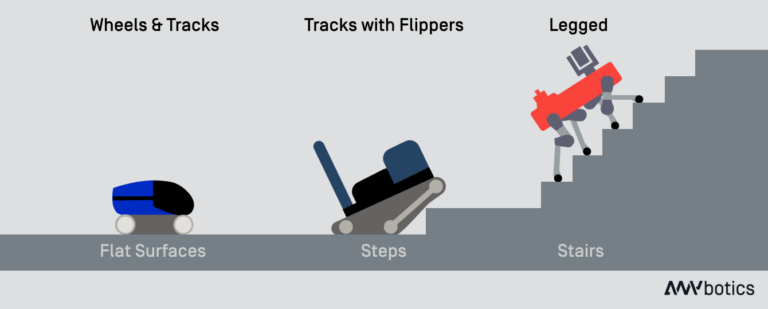
Besides their physical capabilities, the revolutionizing value of industrial inspection robots, and their probably greatest application, is the ability to collect accurate, high-quality data from hundreds of inspection points. This data can often be integrated with third-party software to manage assets, create a digital twin of your facility environment, and accumulate data for predictive maintenance and other analysis.
This data collection ability is revolutionizing how industries operate regarding workers’ safety and efficiency. For example, thanks to the data collected by inspection robots, it’s possible to recreate a digital copy (digital twin) of the environment to inspect, allowing operators to conduct rapid inspections of critical situations with a simple click.
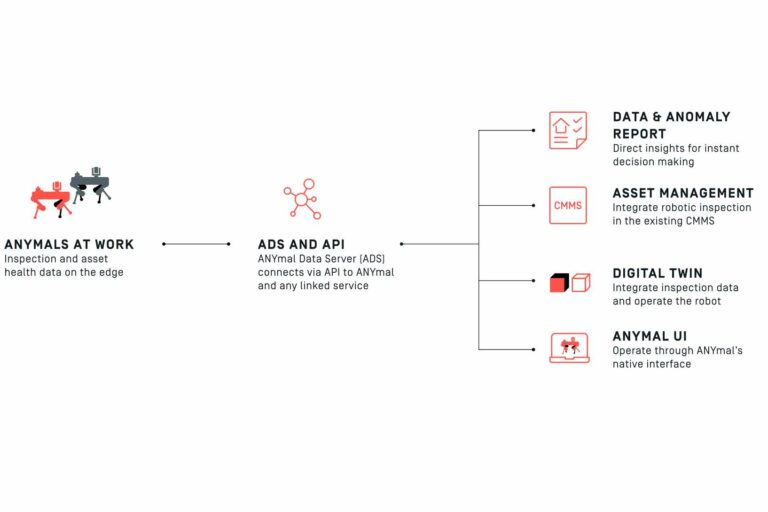
Industrial facilities such as power plants, mining, or nuclear environments, often characterized by a demanding nature, high temperatures, excessive noise, and physical strain that can significantly burden or endanger employees, strongly benefit from this type of robot application.
Looking Ahead
In conclusion, inspection robots are at the forefront of technological innovation and are reshaping the landscape of inspection practices in various industries. From the depths of oil rigs to the heights of wind turbines, these robotic wonders offer unparalleled opportunities to conduct thorough inspections, improve safety standards and increase operational efficiency.
As the industry evolves and undergoes digital transformation, the role of inspection robots will continue to grow. With advances in artificial intelligence, sensor technology and data analysis, the future offers limitless opportunities for further innovation and optimization in inspection processes.
Start your robotic journey with ANYbotics
Get a glimpse of the value ANYmal can unlock
for your business with this 30-minute demo: