Predictive maintenance is a cutting-edge approach that uses advanced algorithms and machine learning to predict equipment failures before they occur: a proactive strategy that differs significantly from traditional preventive maintenance methods and can make a difference in your industrial operations.
Despite the numerous benefits, many companies have been hesitant to fully embrace these strategies in their daily operations because they lack sufficient knowledge about them.
PThis article aims to provide an overview of predictive maintenance and its significant impact on industrial operations: By identifying potential equipment problems, before they lead to failure, companies can avoid costly downtime, ensure smooth and safer operations, and free up time and resources for the maintenance operators.
Table of contents:
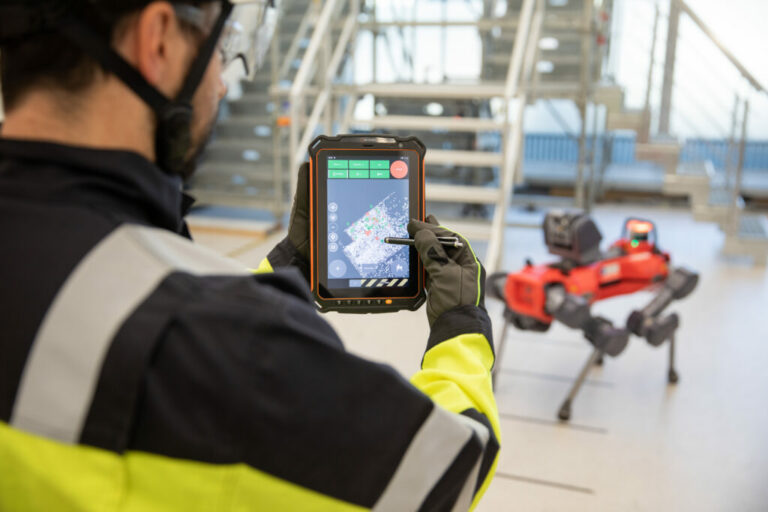
What is Predictive Maintenance?
Predictive maintenance includes using sensors, machine learning, and data analytics to monitor real-time equipment performance and health to predict failures in advance, allowing for timely intervention. This can help extend asset lifespans and avoid unplanned downtime, providing a significant ROI.
The role of AI in predictive maintenance is fundamental to recognizing patterns that indicate potential issues. This requires a large amount of data and frequent checks, which is extremely time-consuming if done manually and potentially impossible on a larger scale.
Some argue that AI cannot replace the proven experience of some maintenance experts who can immediately recognize an anomaly. However, AI should not be seen as a replacement for this knowledge; instead, it allows experts more time for more critical tasks and to replicate and scale this intuitive approach. Given the labor shortage in many industries, it is necessary not to rely solely on the individual experience approach.
Predictive Maintenance vs. Preventive Maintenance
Predictive and preventive maintenance aim to avoid unexpected equipment failures, but they use different approaches and have varying levels of success.
Preventive Maintenance
Preventive maintenance involves regular, scheduled maintenance tasks based on historical data and manufacturer recommendations. It operates on a fixed schedule, regardless of the actual condition of the equipment. For example, changing the oil in a machine every six months, regardless of its current condition, is a form of preventive maintenance.
Predictive Maintenance
In contrast, predictive maintenance, as previously stated, is condition-based and relies on real-time data. Maintenance is only carried out if there are indications of a possible failure. This approach minimizes unnecessary maintenance activities and focuses resources on equipment that really needs attention.
Key Differences Between Preventive and Predictive Maintenance
-
- Scheduling: Preventive maintenance follows a fixed schedule, while predictive maintenance is performed as needed, based on real-time data.
- Cost-Effectiveness: Predictive maintenance is generally more cost-effective because it reduces unnecessary maintenance tasks and prevents unexpected failures.
- Data Usage: Predictive maintenance uses advanced analytics and current data, while preventive maintenance relies on historical data and scheduled time intervals.
Advantages of the Predictive Maintenance approach
- Reduced Downtime: By predicting failures before they occur, predictive maintenance minimizes unplanned downtime, ensuring continuous operations and higher productivity.
- Lower Maintenance Costs: Targeted maintenance activities reduce the need for routine maintenance and the associated labor costs.
- Longer Equipment Lifespan: Addressing issues before they cause significant damage can extend the life of the equipment.
- Improved Safety: Predictive maintenance helps to anticipate failures that could jeopardize worker safety.
Challenges of Predictive Maintenance
There are two main challenges to implementing a predictive maintenance strategy:
- Identify the key indicators to monitor for each asset: Different assets have different failure modes and maintenance needs, so a one-size-fits-all approach doesn’t work. This is one of the reasons why using IoT sensors could be impractical and costly compared to other solutions for predictive maintenance, such as mobile inspection robots.
- Collect consistent data: Inconsistent data or gaps may lead to inaccurate predictions. Automating inspections and monitoring systems ensures data consistency, allowing preventive detection of anomalies.
Implementing Predictive Maintenance with Inspection Robots
One way to conduct predictive maintenance is by using fixed sensors. While this method is an improvement over manual inspections, it has limitations. Fixed sensors, being static, capture only partial data. Additionally, they must be manually placed, and industrial environments often have critical assets in hard-to-reach or hazardous areas.
For these reasons, mobile inspection robots like ANYmal pioneer predictive maintenance and reduce some associated challenges.
It performs an autonomous inspection routine to collect the correct data at the right time. In addition, a single robot equipped with measurement payloads can reliably and consistently collect different data types from assets at various locations in your facility.
How Inspection Robots Facilitate Predictive Maintenance
-
-
-
- Data Collection: Inspection robots gather real-time data from equipment, including visual, thermal, gas, and acoustic data. This data is crucial for analyzing the condition of the machinery.
- Accessibility: Robots can access areas that are dangerous or difficult for human workers, such as inside pipelines,high-temperature, and high-voltage environments.
- Accuracy: Equipped with high-precision sensors, robots can detect minute changes in equipment conditions that can be missed by human inspectors.
- Consistency: Robots provide consistent inspection results, eliminating the variability that can occur with human inspections.
-
-
ANYmal – Significantly contributing to chemical facility’s uptime
W.R. Grace is transitioning the Düren Chemical plant (Germany) from planned to preventive maintenance with ANYmal from ANYbotics as a critical component. In operations, ANYmal achieved a 1.5% increase in plant uptime.
Advancing Predictive Maintenance for Industrial Efficiency
Predictive maintenance, enhanced by inspection robots, represents a significant advance in asset-intensive industries. Using real-time data and advanced analytics, companies can predict and prevent equipment failures, reduce costs, and improve safety and efficiency. As technology develops, predictive maintenance will become an even more critical factor in maintaining the reliability and productivity of industrial operations.
Start your robotic journey with ANYbotics
Get a glimpse of the value ANYmal can unlock
for your business with this 30-minute demo: