Industrial inspections are a cornerstone of asset integrity, operational safety, and plant efficiency. Yet, the reliance on manual rounds exposes facilities to hidden costs: inconsistent data, safety risks, and preventable downtime. Autonomous inspection robots, like ANYmal, offer a measurable return on investment (ROI) by collecting consistent, high-quality data at scale—transforming inspections from a cost center into a source of competitive advantage.
Key Takeaways
- Manual inspections miss early warnings—creating blind spots, safety risks, and costly unplanned downtime.
- Robots inspect more often, capturing consistent, high-quality data that human teams can’t match.
- Proven ROI across industries: Cement, wind, and chemicals save $ 300 K+ in reduced downtime and energy costs.
- Turn inspections into intelligence with sensor fusion, historical data, and predictive maintenance insights.
- Estimate your savings now with the ANYbotics ROI calculator —customized for your plant’s specific operations.
Manual Inspections: A Persistent Blind Spot in Industrial Operations
While essential for safety and performance, manual inspections fall short in four key areas:
- Inconsistent frequency: Assets may only be checked monthly or quarterly, leaving critical warning signs undetected.
- Subjectivity: Human observations vary, creating inconsistent reporting and limited value for trend analysis.
- Reactive process: Findings often trigger late-stage interventions, leading to unplanned downtime.
- Labor-intensive & hazardous: Workers face risks in extreme environments such as confined spaces, heights, or toxic zones.
Example: A cement plant relying on monthly thermography missed the early signs of an overheating driveshaft coupling—caught only when ANYmal inspected the area daily.
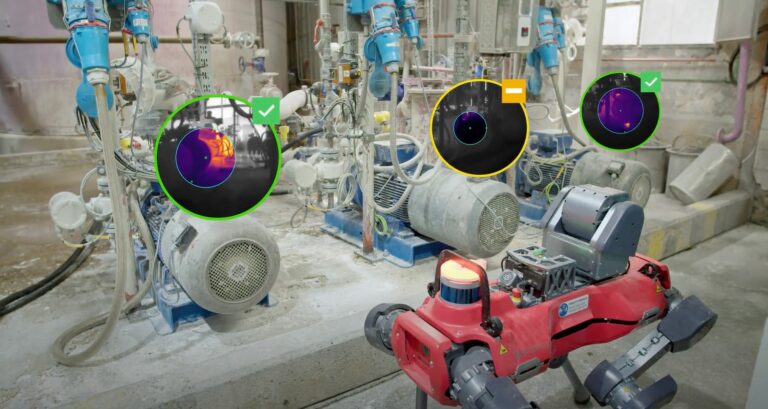
Understanding the True Cost of Manual Inspection
Manual inspections may seem straightforward on the surface, but they carry hidden operational and financial costs that accumulate over time and silently erode efficiency. These traditional methods—still widely used in many industrial facilities—are reactive, labor-intensive, and prone to error.
Some of the most common, yet overlooked, drawbacks include:
- Unnoticed early-stage failures, such as minor leaks, abnormal vibrations, or gradual temperature increases, which escalate into major failures if left undetected.
- Delayed maintenance response, often due to low inspection frequency or missed anomalies, resulting in costly breakdowns and unplanned downtime.
- Lost productivity, as reactive repairs interrupt production schedules and require emergency resource allocation.
- High labor costs, since manual inspections demand regular rounds by skilled personnel, especially challenging with ongoing labor shortages.
- Poor data utilization, with insights often trapped in inconsistent logs, handwritten notes, or siloed digital tools that offer limited visibility across teams.
These inefficiencies are compounded across large facilities and complex operations. Robotic inspection completely redefines the economics of condition monitoring by automating routine rounds. Solutions like ANYmal can perform daily—or even hourly—autonomous inspections, consistently capturing critical data without increasing staffing or exposing personnel to risk. The result is a safer, leaner, and far more proactive maintenance strategy.
Robotic Automation: Transforming Inspection into a High-Frequency, Data-Rich Process
Autonomous robots like ANYmal are revolutionizing industrial inspections by delivering high-frequency, high-fidelity data that manual rounds simply cannot achieve. Equipped with a suite of advanced sensors, ANYmal captures comprehensive, multi-dimensional insights that support safer, smarter, and more scalable operations.
Its sensor payload includes:
- Thermal cameras that continuously monitor surface temperatures to detect overheating before damage escalates.
- Acoustic sensors that identify subtle changes in sound patterns—early indicators of mechanical issues like bearing wear or misalignment.
- High-resolution visual cameras that spot visible signs of deterioration, such as corrosion, cracks, or oil leaks.
- Gas detectors that track emissions and leaks, enabling proactive intervention to protect safety and compliance.
- AI-powered analytics that contextualize the data, highlight anomalies, and automatically trigger work orders based on predefined thresholds.
Every data point is geo-tagged, time-stamped, and asset-linked, creating a traceable and objective digital record. This information is seamlessly processed and visualized within the ANYbotics Data Navigator, a platform that gives maintenance teams real-time access to inspection results, trend histories, and actionable insights—making it easier to plan interventions and prioritize critical assets.
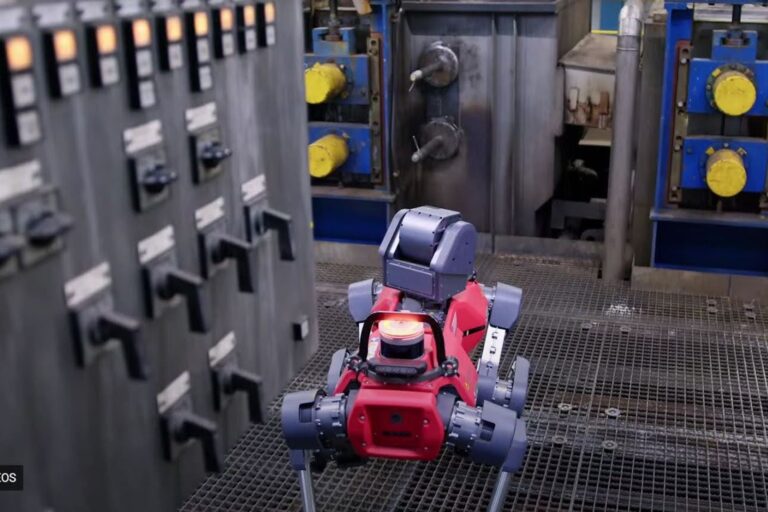
European Cement Leader Avoids $300K Downtime in 12 Months
At a large cement production facility in Greece, manual inspections were failing to keep pace with the operational demands of the site. Due to the plant’s complexity and sheer size, operators struggled to conduct regular checks on all critical equipment. This meant that essential assets—like blowers, compressors, and pumps—were often left unmonitored between scheduled rounds, increasing the risk of unnoticed degradation and costly failures.
To address these gaps, the facility deployed ANYmal, enabling consistent, autonomous inspections that dramatically increased data coverage and inspection frequency. During each round, the robot captured:
- Thermal images to identify overheating components.
- Acoustic data to assess the mechanical health of equipment.
- Visual records of asset condition and potential leaks.
This automated approach empowered maintenance teams with early-warning insights, such as detecting a pump bearing operating above optimal temperature or identifying compressed air leaks—an often-overlooked source of energy loss in cement plants.
By shifting from reactive to predictive maintenance, the facility achieved:
-
- Over $100,000 in annual energy savings
- More than $300,000 saved by avoiding unplanned downtime
- A significant reduction in human exposure to hazardous areas, including the preheater tower and rotary kiln zone
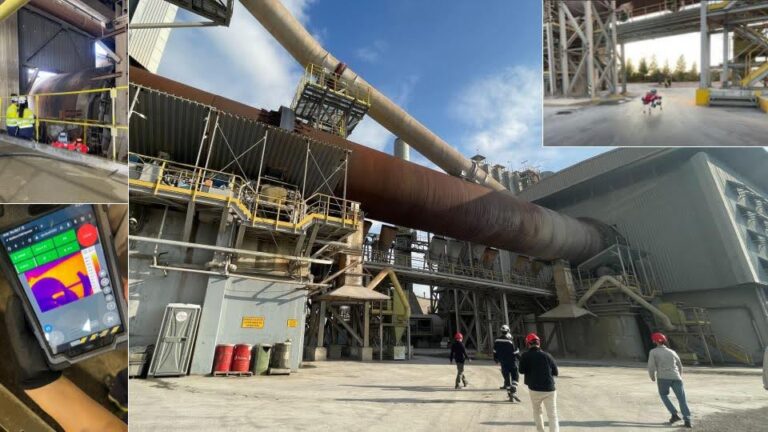
Offshore Wind: 250%+ ROI and Safer Remote Operations
For Equans, a global leader in sustainable energy solutions, managing inspections at an offshore wind farm came with major logistical and financial challenges. Every inspection required dispatching a crew transfer vessel (CTV)—a costly process often delayed by poor weather conditions. Compounding the problem, over 70% of turbine alarms were false positives, unnecessarily triggering offshore interventions.
The implementation of ANYmal changed the game. Permanently stationed on the turbine platforms, the robot carried out autonomous inspections around the clock, unaffected by sea conditions or daylight. Its inspection capabilities included:
- Temperature monitoring of key components to prevent overheating
- Visual checks to identify structural issues like corrosion or cracks
- Gas and environmental readings to ensure compliance and detect leaks
- Acoustic sensing to spot early signs of mechanical failure through subtle sound patterns
With ANYmal’s teleoperation functionality, onshore teams could remotely verify alarms in real-time—eliminating unnecessary CTV deployments and significantly lowering operational costs.
The impact was immediate and substantial:
- The robot paid for itself in under eight months
- The projected three-year ROI exceeded 250%
- Operational risk was minimized, improving crew safety and system reliability
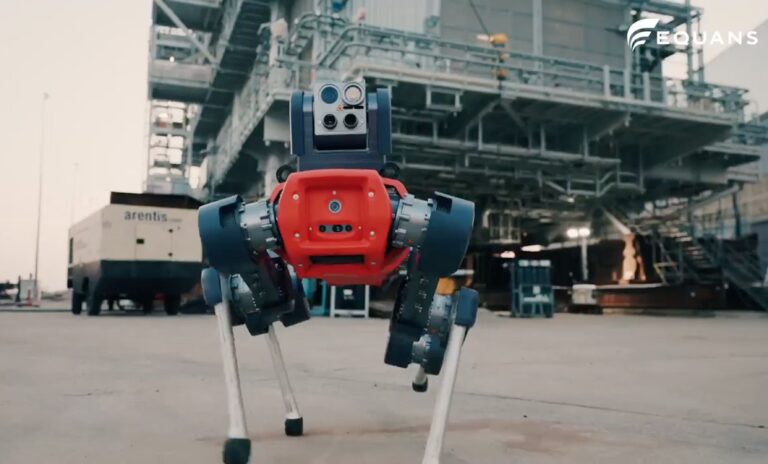
Chemical Manufacturing: >190% ROI and 1.5% Uptime Increase
At Grace Silica, a global manufacturer of specialty chemicals, routine inspections were limited to a select group of high-priority assets fitted with dedicated sensors. The majority of medium-critical equipment—such as pumps, motors, and gearboxes—relied on infrequent manual inspections. This left significant visibility gaps in their asset monitoring strategy.
With ANYmal integrated into their operations, Grace Silica expanded their monitoring coverage from a few dozen assets to over 1,000. The robot performed multiple inspections per day, often revisiting certain assets seven times daily. Equipped with high-precision thermal, visual, and acoustic sensors, ANYmal detected anomalies early and enabled actionable insights.
In one example, the robot identified a steady rise in temperature in an oil pump servicing several production lines. The data allowed the maintenance team to investigate and discover a buildup of dust on the cooling fins. Timely cleaning brought temperatures back to safe levels, preventing insulation breakdown and bearing damage.
As a result of deploying ANYmal, the plant saw:
- A measurable 1.5% increase in uptime
- A shift toward data-driven, predictive maintenance
- A return on investment of over 190% in less than 12 months
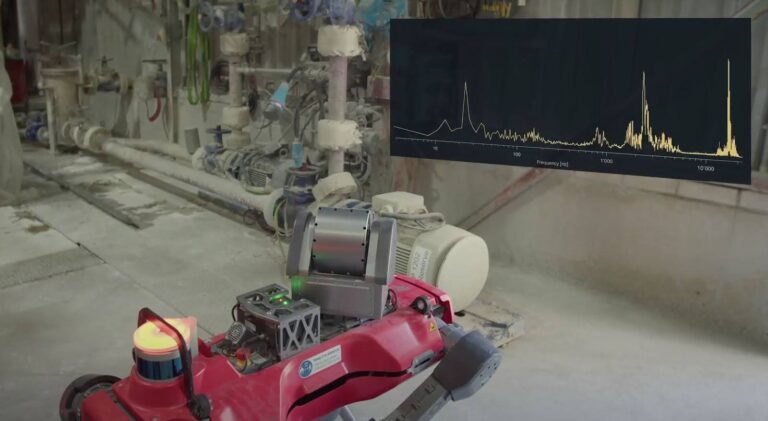
Measuring ROI: A Structured Approach
When evaluating the return on investment (ROI) of inspection automation, technical decision-makers should focus on these key areas:
- Labor Efficiency: Calculate the savings from reducing the hours spent on manual inspections and the increased value generated by redeploying skilled personnel to more strategic reliability tasks.
- Downtime Avoidance: Quantify the financial benefit of each unplanned equipment stoppage that can be prevented through proactive monitoring and early intervention.
- Safety Improvement: Assess the reduction in risks and potential costs associated with personnel working in hazardous environments due to automated inspections.
- Energy Savings: Determine the potential cost reductions from identifying and addressing issues like leaks, thermal inefficiencies, and other often-overlooked operational energy losses.
- Data Quality Gains: Evaluate the benefits of transitioning from inconsistent and infrequent manual records to consistent, high-frequency data collected by multiple sensors, which can lead to more informed decisions.
To simplify this analysis, ANYbotics offers a dedicated ROI Calculator. This tool allows plants to enter their specific operational parameters and receive a custom savings projection backed by real-world case data.
From Inspections to Intelligence
The true power of autonomous inspection goes beyond just making operations more efficient. It lies in establishing a continuous, high-quality data foundation that fundamentally changes how industrial equipment reliability is managed.
Each inspection performed by robots like ANYmal doesn’t just record the current condition of machinery; it contributes to an expanding historical dataset. This growing data pool enables much more than basic condition monitoring. This constant flow of information from various sensors becomes the foundation for AI-driven anomaly detection, predictive models that forecast failures, and the automatic creation of maintenance work orders. This allows maintenance teams to move away from reacting to breakdowns and adopt fully predictive maintenance strategies, prioritizing risks.
This shift offers significant advantages beyond saving money for businesses grappling with increasing operational expenses, aging equipment, and the need to enhance safety and sustainability. It builds long-term operational resilience, creating more innovative and transparent processes that are better prepared to adapt to evolving regulations, economic conditions, and environmental demands. Companies that embrace this data-driven future will reduce costs and improve equipment reliability and gain a sustainable competitive edge.
Discover Your ROI Potential
How much can robotic inspection save your facility?
Use our interactive ROI Calculator to quantify your potential cost savings, reduced downtime, and efficiency gains with ANYmal—tailored to your operations.